The Rise of the Mobile Factory: How Technology Drives Manufacturing ROI
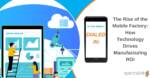
The roar of the assembly line used to define manufacturing. Today, however, a new sound is growing louder: the quiet hum of mobile technology. Gone are the days of paper-based processes and limited communication. Today, a new frontier beckons: the mobile factory.
Sticking to traditional, paper-based processes can lead to a cascade of problems: skyrocketing operational costs due to inefficiencies and errors, missed deadlines from slow production cycles, and compromised worker safety from a lack of real-time information. These issues not only hurt the bottom line but can also damage customer satisfaction.
As the industry undergoes a digital revolution, manufacturers are harnessing the power of mobile devices to unlock a treasure trove of benefits – and a significant return on investment (ROI).
The Price of Staying Still
Traditional, paper-based systems and limited communication tools can lead to a multitude of problems:
- Soaring Operational Costs: Inefficiencies like errors and rework can significantly impact your bottom line.
- Production Delays: Manual processes can slow production cycles, leading to missed deadlines and frustrated customers.
- Safety Concerns: Lack of real-time information and communication can compromise worker safety.
- Quality Issues: Inefficient processes can lead to product defects and increased scrap rates.
These are just a few of the pitfalls of clinging to outdated methods.
Measuring Your Return: The ROI of Mobile Technology
Understanding the true value of a mobile technology investment requires careful measurement. But how is impact quantified? By examining key metrics impacting the bottom line.
Increased productivity is a clear indicator of ROI. How much faster can tasks be completed with mobile solutions in place? Cost reduction is another key metric. How much money can be saved by streamlining operations and eliminating inefficiencies? Improved quality, as measured by reduced defects and rework, directly impacts the bottom line. Finally, consider the impact on customer satisfaction. How do faster response times and real-time order tracking influence customer loyalty and advocacy? These metrics provide a clear picture of a mobile technology investment’s effectiveness.
Unlocking the Benefits: The Power of Mobility in Action
So, how does mobile technology deliver tangible ROI in manufacturing?
Operational Efficiency:
- Real-time Data Access: Mobile devices empower workers with instant access to production data, enabling faster decision-making and problem-solving.
- Streamlined Inventory Management: Mobile barcode scanners and inventory management apps ensure you have the right materials at the right time, reducing stockouts and overstocks.
- Improved Work Order Management: Mobile work order systems streamline task assignment, tracking, and completion, ensuring everyone is on the same page.
- Predictive Maintenance: Mobile apps for predictive maintenance optimize equipment upkeep, preventing downtime and keeping production humming.
Quality Improvement:
- Enhanced Quality Control: Mobile devices enable real-time quality checks, reducing defects and rework.
- Enhanced Traceability: Mobile technology facilitates product traceability, improving recall management and building consumer confidence.
Cost Reduction:
- Reduced Paperwork: Mobile forms and digital signatures eliminate paper-based processes, saving time and money.
- Improved Supply Chain Visibility: Real-time data on inventory levels and supplier performance optimizes logistics and reduces costs.
- Reduced Labor Costs: Mobile technology can automate tasks, freeing up workers for higher-value activities.
Enhanced Customer Satisfaction:
- Improved Customer Service: Mobile devices enable faster response times to customer inquiries and issues.
- Real-time Order Tracking: Mobile apps provide customers with instant updates on order status, building trust and loyalty.
Measuring Success: Quantifying the Impact
To truly understand the return on a mobile technology investment, clear Key Performance Indicators (KPIs) must be established to measure the impact across various operational areas.
Monitor productivity gains, such as increased output and reduced cycle times. Assess the impact on quality by tracking reductions in defects and rework. Evaluate inventory management efficiency through metrics like inventory turnover and carrying costs. Measure the reduction in equipment downtime and maintenance expenses to understand the cost savings. And finally, assess the impact on employee morale and job satisfaction to gauge the overall effectiveness of your mobile technology investment.