3 Ways Your Mobility Solution is Failing in the Warehouse (and How to Fix It)
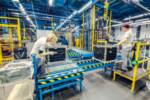
Estimated Read Time: 3.5 minutes
Warehousing and distribution centers are the engine rooms of the global supply chain, powered almost entirely by deskless workers. These frontline teams rely on fast, reliable mobility to scan, ship, stock, and stay connected. But in many facilities, a failing mobility solution hasn’t kept pace with the speed and complexity of the work.
Mobility should accelerate warehouse operations—not become a hidden liability. Here are three of the most common ways mobility is failing deskless teams today—and what you can do to fix it.
1️⃣ The Wrong Tools for the Environment
Consumer-grade devices may be fine for an office, but in the warehouse, they’re a liability. Dust, vibration, glove use, and high-volume scanning demand more than a sleek design. They require purpose-built tools that are rugged, ergonomic, and built for real-world environments.
According to a 2024 Techstep report, non-rugged devices used in harsh conditions fail at a rate of 18–20% per year, compared to just 4–6% for rugged devices. That difference adds up, causing delays, frustrating workers, and disrupting shipments.
But it’s not just about durability. Consumer devices often lack built-in safety features like programmable emergency buttons, location-based alerts, or push-to-talk, all essential in fast-moving environments where quick response can prevent accidents.
The fix: Deploy purpose-built, rugged mobile devices designed to withstand harsh conditions while also enhancing team safety with glove-friendly screens, reinforced construction, and integrated safety tools your workforce can rely on.
2️⃣ Voice and Data Dead Zones
Warehouses are large, metal-filled environments filled with racking, forklifts, and constantly shifting inventory—conditions that often interfere with signal strength and voice clarity. Without enterprise-grade connectivity, even the most advanced mobile devices fall short.
According to a 2024 StayLinked study, over 30% of warehouse workers experience dropped sessions at least once per hour, costing facilities more than $160,000 annually in lost productivity. These connectivity failures can slow workflows, delay shipments, and frustrate already stretched teams.
The fix: Choose enterprise mobility solutions, whether DECT or Wi-Fi, that are purpose-built and optimized for high-noise, coverage-challenged environments. Unlike consumer devices, these solutions offer stronger roaming performance, dedicated voice prioritization, and proven reliability across the entire warehouse floor.
3️⃣ No Visibility = No Accountability
In warehouse operations, downtime isn’t just inconvenient, it’s expensive. But without visibility into how mobile devices are performing in the field, IT teams are often left guessing.
According to Gartner, 45% of IT leaders say mobile device management is one of their top challenges. In warehouse environments where every delay can impact fulfillment, lacking real-time diagnostics and oversight turns even minor device issues into costly disruptions.
The fix: Deploy enterprise mobility platforms that offer centralized monitoring, battery health insights, and remote troubleshooting tools. This enables IT to resolve issues faster, prevent downtime, and keep operations running smoothly.
Get Ahead of the Breakdown
Mobility should drive warehouse performance, not drag it down. If your current solution can’t keep up with rugged demands, fluctuating connectivity, or growing visibility needs, it’s time to reevaluate. Smart mobility isn’t about buying more devices, it’s about deploying the right ones and managing them effectively.
Is mobility failing your warehouse? Fix it with Spectralink. Purpose-built solutions for the speed, scale, and demands of distribution. Learn more: https://www.spectralink.com/workforce-solutions/manufacturing/